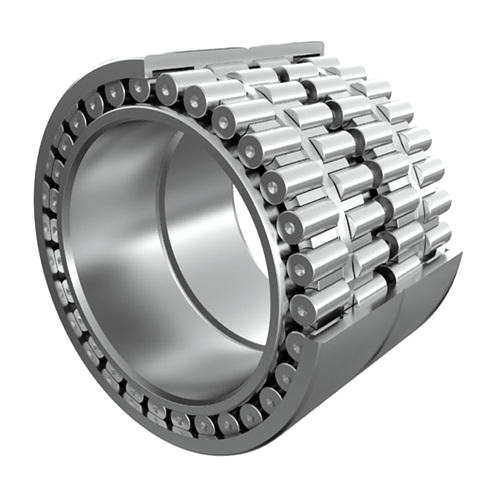
Standard lubrication of four-row cylindrical roller bearings to reduce bearing wear
Standardize lubrication to reduce bearing wear
The lubrication of the bearing is to use the oil film to separate the rolling. Surfaces of relative motion from each other, so as not to fail due. To excessive wear caused by rough point contact. If high attention is pai to the bearing lubrication technology. The roll bearing can be guarantee to maintain. Stable performance and rotation accuracy during the predetermined working life.
In actual production, it is find that there are some problems. In the lubrication of roller bearings:
(1) When the work roll of the rolling mill runs at high speed, it is easy to damage the seal inside the bearing seat. Causing the grease to leak into the emulsion system, polluting the emulsion. And affecting the surface quality of the rolled strip;
(2) Due to the injection of the emulsion under pressure, the emulsion penetrates. Into the roller bearing seat, resulting in emulsification of grease. Failure of the lubrication function easy to cause bearing burnout. And excessive bearing consumption;
(3) The lubricant contains a large amount of water, and the grease softens and changes color. Which makes the rolling surface of the bearing form massive pits;
(4) Part of the heat generated by the bearing needs to be absorb and dissipated by the system itself. For high-speed heavy-duty rolling mills, forced heat dissipation is must. And the bearing lubrication system needs to solve this problem well;
The failure analysis of the roll bearing shows that the normal operation of the roll bearing. Has never been suspend due to fatigue damage caused by normal contact pressure. The failure of the bearing is cause by poor lubrication. Mechanical impurities and moisture intrusion. Moisture in the lubricant, whether dissolved or free. Can have a detrimental effect on the service life of the bearing.
Water can erode the bearing and shorten the service life of the bearing. It can also enter the micro-cracks on the surface of the bearing raceway to cause corrosion. And hydrogen embrittlement, speed up the expansion of the crack. And cause the bearing to peel off in a large area in advance.
The lubrication of rolling mill bearings is divide. Into grease lubrication and oil lubrication. The advantages of grease lubrication are that the lubrication facilities are simple. The grease is not easy to leak, and it has a certain ability to prevent water. Gas and other impurities from entering the bearing. Grease lubrication is use in rolling mills. Rolling mills operating under modern complex, high-precision, heavy-load. High-speed, high-temperature and other working conditions use oil lubrication. Oil lubrication methods include oil mist lubrication and oil-air lubrication.
(1) Grease lubrication
Grease is compose of base oil, thickener and filler. The viscosity of the base oil plays an important role in the lubricating. Performance of the grease. The composition of the thickener has an important influence. On the performance of the grease especially the temperature characteristics. Water resistance, oil separation, etc. The additives are use to enhance the resistance. of the grease. Gasification, anti-rust, extreme pressure and other properties.
Greases are classify according to the types of thickeners. Such as lithium-based and nano-based. Lithium-based grease is used in rolling mill bearings. Lithium-based grease is characterize by good water resistance and high dropping point. And can be use in wet and mechanical parts in contact with water.
Grease is divide into several grades according to its fluidity, that is, penetration. The higher the penetration value, the softer the grease.
The filling amount of grease should be one-third. And one-half of the space between the bearing and the bearing housing. If the grease is add too much, due to the stirring and heating. The grease will deteriorate or deteriorate, and it is not conducive to the. The heat generated during the rotation is dissipate in time. It should only be fill to a third or less at high speed. When the rotation speed is very low, to prevent foreign objects. From entering the bearing, the housing space can be fill.
The service life of lubricating grease is limit. its lubricating performance decreases during use. And the wear also increases , so it must be replaced every certain time. The replenishment period of the grease is relate to the structure. Speed, temperature and environment of the bearing, and should be determine. according to the specific working conditions of the enterprise.
When replacing grease, it should be not that greases of different grades cannot be mixe. And the mixture of greases containing different types of thickeners. will destroy the structure and consistency of the grease. After some grease is completely removed, add new grease.
The purpose of bearing lubrication is to form an oil film on the rolling surface and sliding surface. And form an elastic hydrodynamic lubricating oil film between the metal surfaces. When the lubricant is select , the lubricant is clean enough. And the rotation speed, temperature, and load are appropriate. the bearing service life will far exceed the calculated life.
, the reasonable selection of the lubricant. Is very important to the service life of the roller bearing. The selection of grease should follow the following points:
①The higher the rotational speed, the grease with greater penetration should be use;
②When the ambient temperature is low, apply a large amount of grease;
③ When the ambient temperature is high, use a grease with a higher dropping point;
④ It must have strong water resistance. And sodium-based fat cannot be use, which is easy to emulsify;
⑤The cleanliness, anti-corrosion, water content and oil content.
Of grease should all pay attention to its indicators.
(2) Oil mist lubrication
Oil mist lubrication is a high-efficiency bearing lubrication method. Oil mist lubrication uses compressed air as the power to atomize the oil to produce. A dry oil mist with a particle size of about 2 μm like smoke. And then transport it to the lubrication part through the pipeline. At present, in metallurgical enterprises, oil mist lubrication devices are use. for the lubrication of large, high-speed and heavy-duty rolling bearings.
Compared with other lubrication methods, oil mist lubrication has many unique advantages:
①The oil mist can be disperse with the compressed air to all the friction parts that need to be lubricate. Good and uniform lubrication effect can be get;
②The specific heat of compressed air is small and the flow rate is high. so it is easy to take away the heat generated by friction;
③It reduces the consumption of lubricating oil;
④Because the oil mist has a certain pressure (2~3KPa), it can play a good. Sealing effect and avoid the intrusion of external. impurities and moisture into the friction pair.
oil mist lubrication also has some shortcomings. When choosing, you should pay attention to:
①The discharged compressed air contains 20% to 50% of suspended oil particles. which pollutes the environment and is detrimental to the health of operators. , it is necessary to add a ventilation and mist removal device;
② Must have a set of compressed air system;
③It is only suitable for lubricating oil with lower viscosity, and the atomization. rate of lubricating oil with high viscosity is low;
④Compared with oil and gas lubrication, it has poor adaptability in high speed. high temperature and occasions where the bearing is attacke by stolen goods. water and organic chemical hazards;
⑤ The use rate of lubricants is low, only about 60%. Compared with oil and gas lubrication, the oil consumption is large. And the oil supply is regulated, so it is impossible to supply oil.
(3) Oil-air lubrication
Oil-air lubrication is the continuous action of compressed air. which drives the lubricating oil to flow. Along the inner wall of the pipeline and forms a vortex-like oil-air mixture. (oil and air are not fused or atomized). Into the lubrication point in the form of fine oil droplets, compressed air. Continuous supply, oil is supply ; compared with oil mist lubrication. It has the following advantages. Also to the lubrication and cooling function of oil mist lubrication:
①Suitable for high speed, high temperature, heavy load and occasions. Where the bearing is attack by stolen goods, water and organic chemical hazards;
②Because the oil in the oil-air lubrication is not atomized, but is transport. To the lubricating part by the compressed air in the form of oil droplets. The oil-air lubrication system can deliver lubricating oil with various properties. And is not limited by the viscosity of the lubricating oil;
③In oil-air lubrication, oil and gas can be adjust to meet the requirements. Of each lubrication point by adjusting the amount of oil and compressed air;
4. Only air is emit to the atmosphere, and it does not pollute the environment;
⑤The pressure of the lubricating cavity is determine by the compressed air. And the high pressure of the inner cavity is beneficial. To prevent dust and other impurities from entering;
⑥Complete monitoring means and high degree of mechatronics;
⑦The system has few moving parts, reliable operation and low maintenance.
Its disadvantage is that the one-time investment is large. More roller bearing into: tradebearings